MATHDES
Mathematical Design, Modelling and Simulations
Mathematical Design, Modeling, and Simulations (MATHDES) group works on the design, analysis, implementation, and optimization of numerical schemes for mathematical models arising from real-life applications.
Principal Investigators:
Michael Barton and David Pardo
Our research spans areas of Deep Learning, Inverse Problems, Finite Elements, Massive Computations, Numerical Analysis, Geometric Modeling, Computer Aided Design, and Modeling of Manufacturing Processes. We work in close interaction with industrial partners and institutions to promote transfer of knowledge and obtain feedback from real-life applications.
We currently work on three European Projects:
(a) a FET-OPEN project on Analysis, Design, and Manufacturing using Microstructures ADAM^2, which aims at revolutionizing the design-analysis-manufacturing pipeline, coordinated by Michael Barton; (b) a Marie Curie RISE Action MATHROCKS, intended to improve and exchange interdisciplinary knowledge on applied mathematics, high performance computing, and geophysics, coordinated by David Pardo; and (c) the European NextGenerationEU project IA4TES, funded by the Spanish Ministry for Economic Affairs and Digital Transition and led by Iberdrola, for structural health monitoring and assessment of remaining useful life of offshore wind platforms.
We collaborate with multiple prestigious institutions and industrial partners, including The University of Texas at Austin (USA), Stratasys LTD (Israel), INRIA (France), Hutchinson S.A. (France), Seoul National University (South Korea), Technion - Israel Institute of Technology (Israel), MacQuaire University (Australia), Ecole Polytechnique Federale de Lausanne (Switzerland), Curtin University (Australia), Technical University of Wein (Austria), King Abdullah University of Science and Technology (Saudi Arabia), Software Competence Center Hagenberg (Austria), Pontifical Catholic University of Valparaíso (Chile), Pontifical Catholic University of Chile, National University of Colombia, Central University of Venezuela, University of Buenos Aires (Argentina), Barcelona Supercomputing Center (Spain), Polytechnic University of Catalunya (Spain), University of Barcelona (Spain), University Charles III of Madrid (Spain), Tecnalia (Spain), Trimek S.A. (Spain), and University of the Basque Country (UPV/EHU).
This BCAM group has strong collaboration ties with the sister UPV/EHU Group MATHMODE.
In particular, we are currently involved in the following research projects:
Deep Learning Algorithms for Inverse Problems:
We study and develop Deep Learning methods to interpret (invert) in real-time elasto-acoustic and electromagnetic measurements. To achieve this objective, we design and implement proper Deep Neural Network architectures, loss functions, and error control algorithms enabling us to efficiently approximate physically meaningful inverse solutions.
Massive Finite Element Simulations:
We develop a set of numerical Galerkin-based methods for producing massive synthetic datasets for training Deep Neural Networks. Some examples include variants of Isogeometric Analysis, Dimensionality Reduction Algorithms, Reduced Order Models, Proper Generalized Decompositions, and hp-Adaptivity.
Geometric Modeling:
We model manufacturing processes such as 5-axis Computer Numerically Controlled (CNC) machining, see Fig.1, hot-wire cutting, or hybrid (additive and subtractive) manufacturing.

Fig. 1: 5-axis flank machinability of a reference surface (dark) using various machining tools (green). The tool-paths that meet fine machining tolerances are shown as ruled surface (motions of the tool axis, yellow).
Manufacturing Applications:
In collaboration with the High Performance Manufacturing Group (UPV/EHU), we design path-planning algorithms for multi-axis CNC machining. An example of a simulation of 5-axis flank milling with a custom-shaped tool is shown in Fig. 2. The tool and its motion are both unknowns in our optimization-based framework. Manufactured result (blisk) machined with our algorithm using a conical tool is shown in Fig. 3.
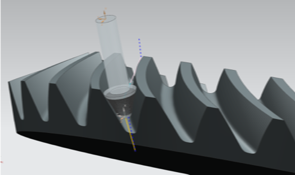
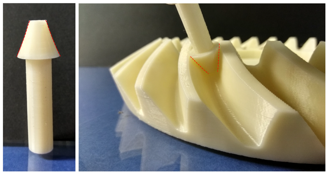
Fig. 2: Simulation of path-planning for 5-axis double-flank CNC machining of a spiral bevel gear using a custom-shaped milling tool, (left). The 3D-printed prototype of the designed tool is shown in right.
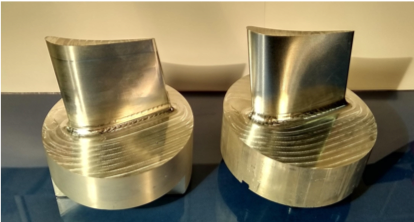
Fig. 3: Finishing of the blisk blade using the state-of-the-art software (Siemens NX, left) and our algorithm (right). Additionally, to higher accuracy (not visible), observe the smooth light reflection in our result, that is due to negligible distance error between the neighboring milling paths.
Geophysical applications:
We employ advanced numerical simulation and inversion methods to characterize the Earth´s subsurface, see Fig. 4. This is critical in several applications, such as (a) the prospecting of water, precious minerals, and hydrocarbons, (b) earthquake prediction and seismic hazard estimation, (c) seismic monitoring, (d) mine detection, (e) geothermal energy production, and (f) management of CO2 sequestration at the industrial scale that is needed to abate the global climate change problem.
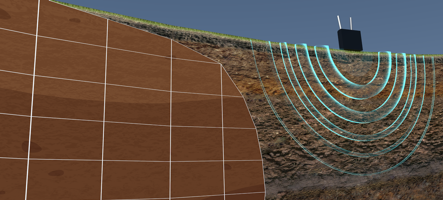
Fig. 4: Controlled Source Electromagnetic Measurements for Earth Exploration
Offshore Wind Energy application:
We design Deep Neural Network architectures as a support of the design and operation of emerging technologies for offshore wind energy applications in three areas: (a) for accelerating CFD simulations using OpenFoam for analysing the hydrodynamics of support structures; (b) for structural health monitoring of components (mooring systems, power cables) in offshore floating platforms (see Fig. 5).; (c) real-time control of offshore wind energy farms for Fault Detection and Fault Tolerant Control.

Fig. 5: Autoencoder architecture for Structural Health Monitoring of Floating offshore wind components
Fault detection and identification for control systems in floating offshore wind farms: A supervised Deep Learning methodology
Fernandez-Navamuel, A.; Peña-Sanchez, Y.; Nava, V. (2024-10-15)
This study employs a data-driven Fault Detection and Isolation (FDI) methodology in Floating Offshore Wind Turbine (FOWT) farms. The main objective of the work lies in classifying faults impacting the components of the contr...
Probabilistic Topology Optimization Framework for Geometrically Nonlinear Structures Considering Load Position Uncertainty and Imperfections
Habashneh, M.; Ghodousian, O.; Fathnejat, H.; Movahedi, M. (2024-12-01)
In this manuscript, a novel approach to topology optimization is proposed which integrates considerations of uncertain load positions, thereby enhancing the reliability-based design within the context of structural engineeri...
Acoustical features as knee health biomarkers: A critical analysis
Kechris, C.; Thevenot, J.P.R.; Teijeiro, T.; Stadelmann, V.A.; Maffiuletti, N.A.; Atienza, D. (2024-12-01)
Acoustical knee health assessment has long promised an alternative to clinically available medical imaging tools, but this modality has yet to be adopted in medical practice. The field is currently led by machine learning mo...
How to Count Coughs: An Event-Based Framework for Evaluating Automatic Cough Detection Algorithm Performance
Orlandic, L.; Dan, J.; Thevenot, J.P.R.; Teijeiro, T.; Sauty, A.; Atienza, D. (2024-01-01)
Chronic cough disorders are widespread and challenging to assess because they rely on subjective patient questionnaires about cough frequency. Wearable devices running Machine Learning (ML) algorithms are promising for quant...
Damage identification in bridges combining deep learning and computational mechanic
CL file
Datasets (Zenodo) for the paper "Manufacturing of screw rotors via 5-axis double-flank CNC machining"
Authors: Michael Barton, Michal Bizzarri
License: Zenodo
CL file
Datasets (Zenodo) for the paper "Geometry and tool motion planning for curvature adapted CNC machining"
Authors: Michael Barton, Michal Bizzarri, Oleksii Sliusarenko, Florian Rist, Helmut Pottmann
License: Zenodo